- insoles.ai Weekly O&P Roundup
- Posts
- Behind the Insole: How Our Custom Orthotics Are Crafted
Behind the Insole: How Our Custom Orthotics Are Crafted
By: Eric Tilly, 3D Print Farm Lead
At insoles.ai, we enable you to scan your patients feet with any device, anywhere, in 30 seconds — without downloading an app or buying a sensor. We then deliver your custom orthotics in 7 days, guaranteed.
Our commitment lies in the intersection of advanced orthotic technology and evidence-based health solutions. In this detailed overview, we’ll explain the process that shapes every custom insole we produce, aiming to provide therapeutic support with each step your patients take.

Graphical Representation of What I Do @ insoles.ai
At the core of our operation is our custom design software for clinical-grade 3D foot-reconstruction, refined to integrate the optimal s-curve, arch height, heel cup, and forefoot shape as standard customizations. Our 3D-printed foot orthotics meet full compliance standards and can even be adapted by practitioners in clinical settings — reflecting the precision of our printing methods. Our 3D printed diabetic orthotic is as adjustable as a traditional cork insoles!
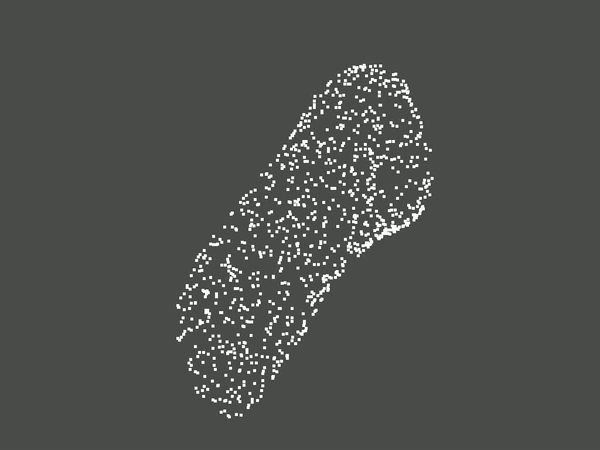
Our Custom Design Software Allows For Granular Modifications By Clinicians
Our design and production are informed by continual feedback, such as the adaptation required for patients’ differing arch heights. Testing with 50+ clinics has led us to create custom printing profiles, enabling a standardization of clinician-preferred insole types and the versatility to adjust to specific requests. InsolesAI supports build-in specialty add-ons such as: Morton extensions, UCBL, offloads, Whitman specialty style, heel lifts, wedges, etc.
This capacity to tailor, down to integrating specialty add-ons or adjusting for emerging trends, ensures our insoles not only maintain foot structure but also provide targeted relief.

When We Say Custom Insoles, We Really Mean It!
Our advanced 3D printing process translates orthotic designs from digital models to physical products with unmatched precision. Each layer is engineered to align with the complex morphology of an individual’s foot. Our technical advancements ensure we deliver orthotics with an efficiency that allows for a remarkable one-week turnaround time. Through comprehensive testing, we have perfected the print profile for each insole, utilizing the unique properties of flexible TPU filament and the capabilities of Fused Deposition Modeling (FDM) technology.

Inside Look At Our Custom-Built R&D Print Farm — insoles.ai Manufactures Products In-House @ Peoria, Illinois. USA!
The printers themselves have been custom-modified to operate at elevated temperatures and accelerated speeds, a necessity for the material manipulation that grants our insoles their signature balance of robust structure and responsive flexibility. Not only can we replicate traditional orthotic manufacturing processes, but also to embrace the versatility required to meet precise, clinician-specified customizations detailed in patient order forms.

insoles.ai-Designed Dashboard to Guarantee Quality Control Along Every Step
Our stringent quality assurance protocols are the backbone of our manufacturing excellence. We ensure that each custom orthotic insole undergoes comprehensive checks for durability and therapeutic efficacy before it reaches the user. We fine-tune the design, carefully cross-referencing all specifications against the order form to guarantee a perfect alignment with the client’s needs. Post-printing, each insole is subjected to a rigorous quality check, leveraging technology to track the progress. With iPads linked to our custom-designed dashboards, our staff monitors every stage, from initial design adaptation to the final cleaning, assuring that each insole not only meets but surpasses our standards.
Our packaging and delivery process is another area where we go beyond the industry norm. Each insole undergoes a custom grinding process to fit the individual contours and prescriptions before being securely enclosed in eco-conscious materials. Each order is meticulously hand-labeled, indicating the order type, destination, and recipient’s name, which not only personalizes the experience but also streamlines the delivery. This level of detail ensures that from the moment our insoles leave the production line to the point they reach the hands of the practitioner or the end-user, they embody the highest standards of quality and care that we stand for.

Custom Grinding for Individualized Products
At insoles.ai, the future of orthotic care is being sculpted today with our relentless pursuit of 3D printing mastery. Our path of innovation is charted with advancements like conical slicing, a breakthrough technique allowing us to seamlessly craft complex geometries. We’re integrating artificial intelligence to drive our rolling bed printers, pushing towards a new realm of autonomous manufacturing. With Adaptive Manufacturing Systems (AMS), we’re poised to diversify material use, ushering in a new era of custom orthotic fabrication. These technological strides, coupled with variable infill density, are sharpening the edge of personalized care, ensuring each insole is not just a product, but a testament to precision medicine.
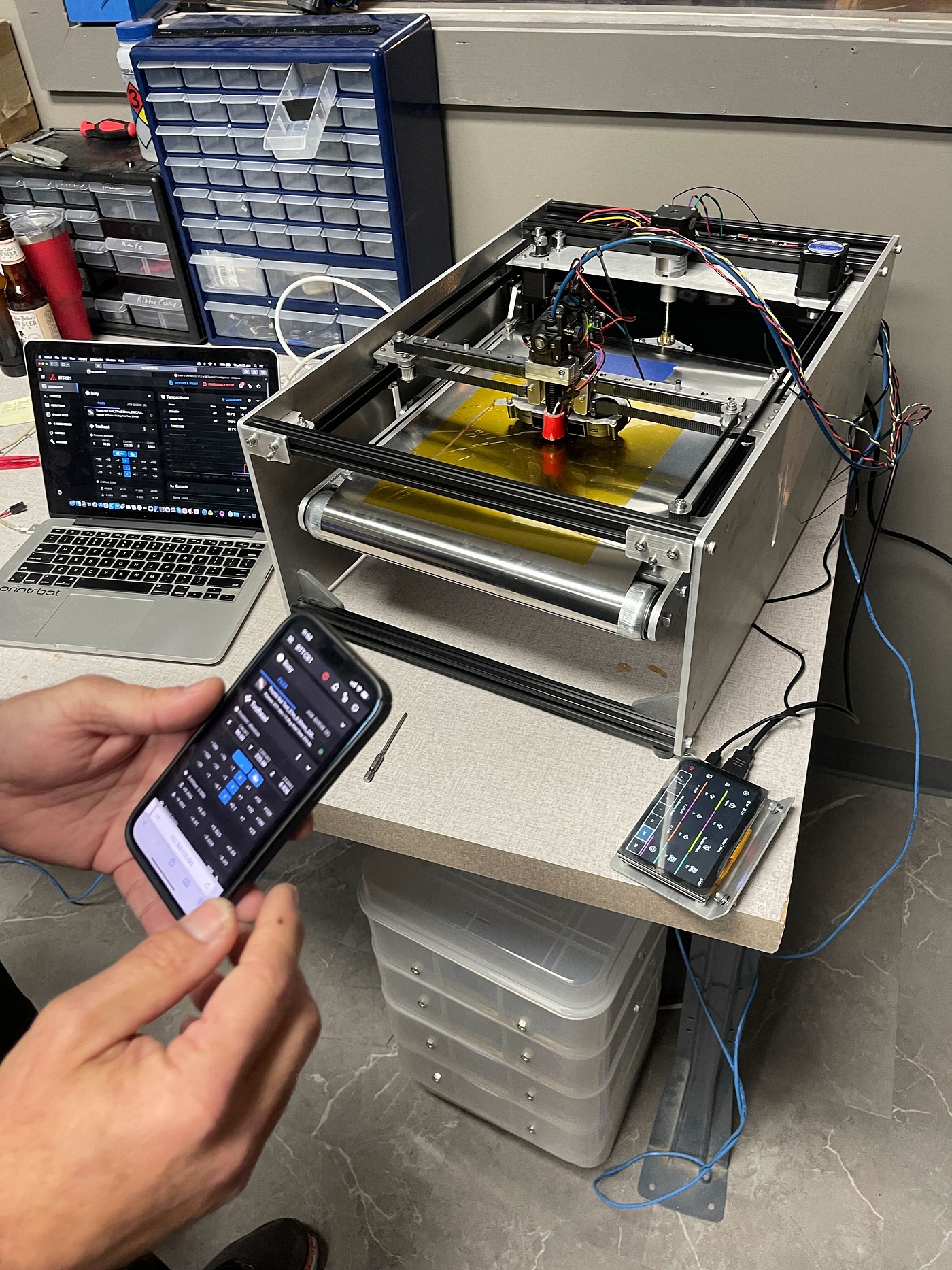
Utilizing Open-Source Capabilities to Become Autonomous
The transformation in orthotic healthcare begins with a conversation, and we at insoles.ai are extending an invitation to be part of this exciting journey. Our journey is one of constant learning, innovation, and genuine passion for enhancing health care through our craft. It’s a privilege to welcome you to this journey, to share our story, and to invite you to join us in shaping a future where every step is supported by the pinnacle of personalized orthotic technology.